Fasteners and Machining: Integrating Accuracy and Strength in Production
Navigating the World of Fasteners and Machining: Methods for Accuracy and Rate
In the complex realm of bolts and machining, the pursuit for accuracy and speed is a perpetual challenge that demands precise focus to information and critical planning. From comprehending the varied selection of fastener kinds to choosing ideal materials that can endure rigorous needs, each action in the process plays a critical role in accomplishing the desired outcome. Accuracy machining strategies further elevate the intricacy of this craft, needing a delicate equilibrium in between technological know-how and innovative approaches. As we look into the methods that can enhance both speed and performance in this domain, the interplay in between high quality control actions and operational excellence becomes an essential prime focus.
Understanding Fastener Kind
When picking bolts for a task, recognizing the different types offered is critical for making sure ideal performance and integrity. Bolts are available in a vast variety of kinds, each developed for particular applications and demands. Bolts are made use of with nuts to hold products together, while screws are flexible fasteners that can be made use of with or without a nut, depending upon the application. Nuts, on the other hand, are inside threaded bolts that friend with screws or bolts, supplying a safe and secure hold. Washers are vital for distributing the lots of the bolt and preventing damage to the product being secured. In addition, rivets are permanent bolts that are perfect for applications where disassembly is not called for. Comprehending the distinctions in between these bolt types is vital for selecting the right one for the work, making certain that the link is strong, sturdy, and trustworthy. By picking the appropriate fastener type, you can optimize the efficiency and longevity of your task - Fasteners and Machining.
Picking the Right Products
Comprehending the relevance of picking the appropriate materials is extremely important in guaranteeing the optimal efficiency and integrity of the picked fastener types discussed formerly. When it pertains to fasteners and machining applications, the material selection plays an essential duty in figuring out the total strength, toughness, corrosion resistance, and compatibility with the designated atmosphere. Various products use differing homes that can considerably affect the efficiency of the bolts.
Usual products utilized for fasteners consist of steel, stainless steel, brass, aluminum, and titanium, each having its one-of-a-kind staminas and weaknesses. Steel is renowned for its high stamina and resilience, making it appropriate for a variety of applications. Stainless-steel supplies outstanding deterioration resistance, ideal for environments prone to moisture and chemicals. Aluminum is corrosion-resistant and lightweight, making it ideal for applications where weight decrease is crucial. Brass is frequently picked for its visual charm and exceptional conductivity. Titanium is understood for its extraordinary strength-to-weight proportion, making it ideal for high-performance applications. Choosing the right material involves thinking about aspects such as strength requirements, ecological conditions, and budget plan restrictions to make certain the preferred efficiency and durability of the bolts.
Accuracy Machining Techniques
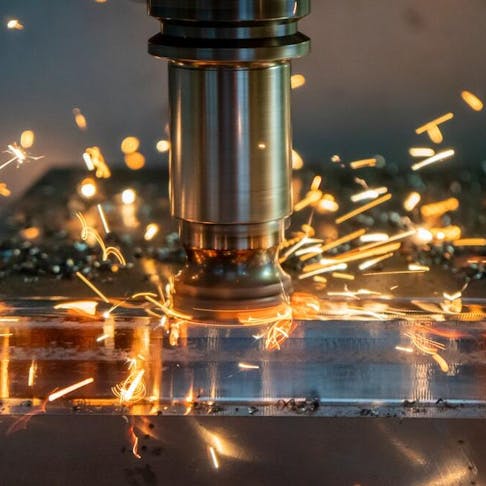
Along with CNC machining, other accuracy methods like grinding, transforming, milling, and drilling play important functions in fastener production. Grinding helps achieve great surface area finishes and limited dimensional resistances, while turning is usually made use of to produce cylindrical components with specific sizes. Milling and boring operations are vital for shaping and creating openings in bolts, ensuring they fulfill specific requirements and feature properly.
Enhancing Rate and Performance
To optimize bolt manufacturing processes, it is necessary to streamline procedures and carry out effective techniques that enhance accuracy machining strategies. One crucial method for improving rate and efficiency is the implementation of lean production principles. By reducing waste and concentrating on continuous enhancement, lean methods help optimize and remove traffic jams process. Additionally, purchasing automation modern technologies can significantly improve production speed. Automated systems can handle repeated tasks with precision and rate, allowing employees to concentrate on even more complicated and value-added activities. Adopting Just-In-Time (JIT) supply management can likewise improve performance by ensuring that the best materials are readily available at the correct time, lessening excess supply and reducing preparations. Promoting a society of cooperation and Get the facts communication among team members can improve general effectiveness by advertising transparency, problem-solving, and advancement. By integrating these methods, suppliers can achieve a balance between rate and accuracy, ultimately enhancing their one-upmanship in the bolt market.
Top Quality Control Procedures
Implementing strenuous quality control steps is critical in making sure the reliability and uniformity click here for info of fastener items in the production process. Quality assurance measures incorporate different stages, beginning from the option of raw products to the last examination of the ended up fasteners. One basic facet of quality assurance is conducting comprehensive material examinations to confirm compliance with requirements. This involves analyzing variables such as material strength, toughness, and make-up to guarantee that the bolts satisfy sector requirements. Furthermore, keeping track of the machining processes is necessary to promote dimensional precision and surface area coating high quality. Using innovative innovation, such as computerized inspection systems and precision measuring tools, can enhance the accuracy and effectiveness of quality assurance treatments.
Routine calibration of equipment and equipment is important to keep consistency in production and make sure that fasteners fulfill the necessary tolerances. Carrying out rigorous methods for recognizing and addressing non-conformities or flaws is essential in protecting against substandard items from getting in the market. By establishing a detailed quality control structure, producers can promote the credibility of their brand and supply bolts that meet the highest possible standards of performance and sturdiness.
Verdict
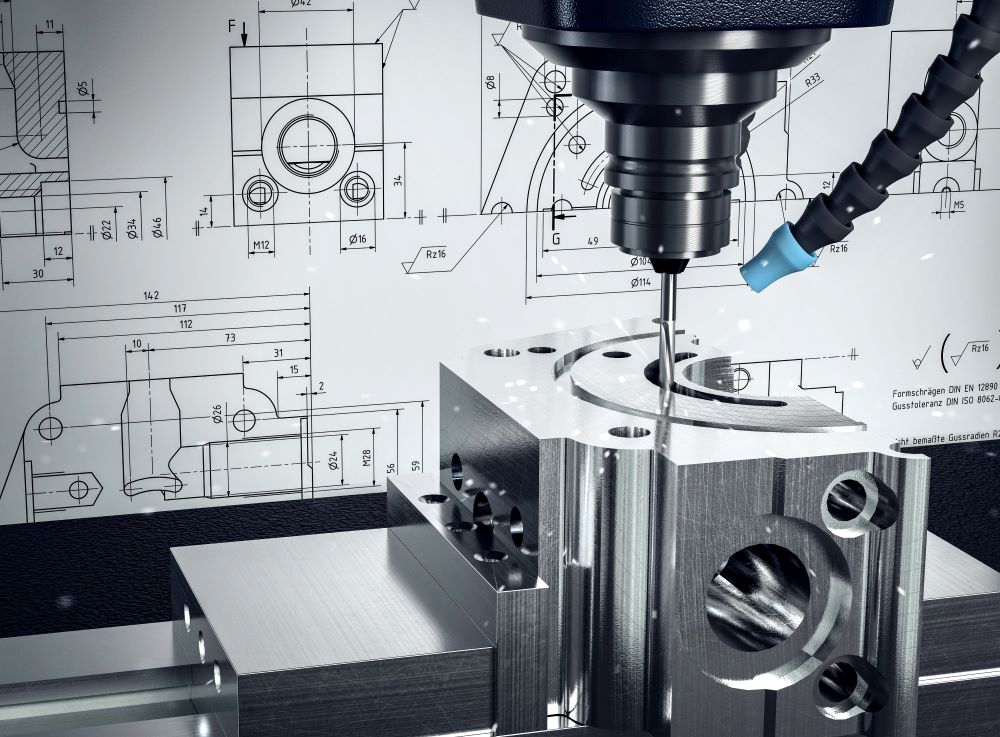
In the intricate realm of fasteners and machining, the pursuit for precision and speed is a perpetual challenge that demands thorough interest to information and strategic planning. When it comes to bolts and machining applications, the product choice plays a crucial role in establishing the total toughness, durability, rust resistance, and compatibility with the intended atmosphere. Precision machining entails different advanced approaches that make sure the tight resistances and requirements needed for fasteners.In addition to CNC machining, other accuracy strategies like grinding, transforming, milling, and drilling play essential functions in fastener production.To enhance fastener production procedures, it is important to simplify operations and execute efficient techniques that enhance accuracy machining methods.